In 2012, Techinservice Manufacturing Group reconstructed Gaisyn Sugar Mill, Zorya Podillya PC, to increase the capacity of the plant from 6,000 tons of beet/day to 8,000 tons of beet/day and reduce the specific steam consumption for production to 28.5 % by weight of beet.
During modernization of the plant the following stations were reconstructed and fully automated:
• The ДС-12 diffusion house installed in 2012 at the mill including beet cutters, chips feeding line, pulp discharge line, condensate collection and withdrawal line has been automated;
• Pulp-press house: pulp-press water pasteurization line has been installed; raw pulp feeding line and pressed pulp discharge lines have been automated.
• Juice purification station: following equipment produced by Techinservice was installed – Briegel-Muller progressive prelimer (designed for a capacity of 10,000 tons of beet/day), lime milk dynamic mixer and 2nd carbonation tank. All main flow pumping units have been replaced by Andritz pumps with hydrodynamic sealing.
• Heating system and evaporating station: the quintuple-effect evaporating station was changed to the sextuple-effect evaporating station with the use of the existing Robert evaporators in the 1st, 2nd, 5th and 6th effects, as the 3rd and 4th effects the direct-flow fallingfilm evaporators of Series ТВП12-4870 and ТВП9-2430 were installed.
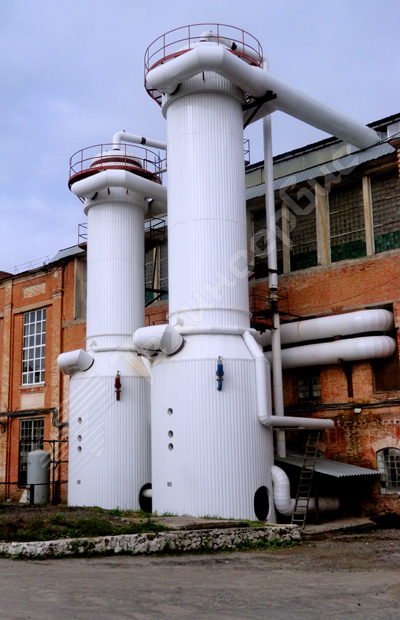
Direct-flow falling film evaporators of Series ТВП
• Condensate circuit is fully assembled on the basis of new multisection condensate collectors produced by Techinservice.
Condensate collector
• For heating products, the new sectional heaters produced by
Techinservice as well as baffle heaters were installed, and the following existing heaters were reconstructed:- Pulp-press water: heat exchanger of Series ТТЖВ83 and heater of Series ТПЖВ83
- Diffuse juice: low-grade steam heater of Series ТПДУ270 – 2 pcs.;
- Limed juice: heat exchanger of the 1st group of Series ТТДС244; heater of the 2nd group of Series ТПДС361; heater of the 3rd group of Series ТПДС244;
Limed juice heaters
- 1st carbonation juice before filtration: existing gas heater of Series ПДС-10-200 was changed from a 10-way heater into 5-way heater;
- Juice before 2nd carbonation: new plate heat exchangers of the 1st group (2 pcs.) have been installed and connected according to the parallel scheme; existing heaters of Series ПДС-10-200 have been connected according to the parallel scheme;
- Juice before the evaporating station: new baffle heater of the 4th group has been installed; 3rd, 2nd and 1st group were composed of existing heaters of Series ПДС-10-200, upgraded from 10-way heaters into 5-way heaters;
Heaters in front of the evaporating station
- Runoffs in the sugar end (green molasses of the 1st product, white molasses of the 1st product; green molasses of the 2nd product): new plate heat exchangers were installed.
Molasses heat exchangers
• The syrup filtering station is mounted on the basis of new TF-150/65 filters with perlite alluvium produced by Techinservice.
Syrup filters
• Melting of brown sugar of the 2nd and 3rd products is carried out by syrup after the evaporating station in the melting mixers of Series TKM-30 and TKM-15 produced by Techinservice.
Sugar melting mixer
• Vacuum pans of the 1st product of Series Л4-ПУ-2А-60 were reconstructed into the vacuum pans of Series ТВА-60 with the installation of a new heating chamber, a discharge cone and circulators produced by Techinservice.
Vacuum pans of the 1st product
• Vacuum pans of the 2nd product of Series Л4-ПУ-2А-60 were reconstructed into the vacuum pans of Series ТВА-60-78 with the installation of a new heating chamber, a discharge cone and circulators produced by Techinservice.
Vacuum pans of the 2nd product
• The seed massecuite system was assembled for the 1st, 2nd and 3rd products on the basis of the new ТВА-60 vacuum pan, massecuite receiving mixer of Series ТПМ40/50 and three pressure massecuite receiving mixers of Series ТМДУ9 produced by Techinservice using Börger pumps.
Magma seed receiving mixers
• Lime gas kiln: the existing furnace No. 2 was extended and increased in diameter and it fully satisfies the plant’s capacity of 8,000 tons of beet/day; the new charge preparation station, new loading and distribution devices produced by Techinservice were installed.
Lime gas kiln Charge preparation station
• Cooling tower: 3 new fan cooling towers were installed.
Cooling tower
Detailed information is given below:
The automatic control system of the diffusion house provides the possibility to control beet feeding, chips consumption, auger speed, pulp discharge and removal, pulp-press water sterilization, feeding of sulfuric acid for sulfitation of feed water, formalin feeding, feed water supply, zone temperature, condensate withdrawal and diffusion juice pumping-out without direct involvement of staff.
Mnemonic scheme of the diffusion house
Adjustment and synchronization of the auger speed is performed by means of two frequency converters in the master-slave mode according to the level of chips in the shaft of the unit, which is changed by two discrete sensors; current load of the upper and lower drives of the diffusion system.
The sterilization circuit of the pulp-press water (PPW) with the use of a rapid heat exchanger and a heater produced by Techinservice heats the water before sterilization and then cools it to a predetermined temperature (72-65 °C).
Mnemonic scheme of the pulp-press house
The existing juice purification station designed for a plant capacity of 8,000 tons of beet/day has been modernized as follows:
1) The new Briegel-Muller progressive prelimer of Series ТППД200 which was mastered for production in 2012, was installed.
Briegel-Muller prelimer
2) Hot liming tank consists of 2 stages: 1st stage is direct flow line (former 1st carbonation muddy juice tank) with the ability to discontinue the flow, 2nd stage is the existing hot liming tank.
3) 1st carbonation boiler consists of 2 stages: 1st stage is the former 1st carbonation boiler; 2nd stage is the former 2nd carbonation boiler.
4) Muddy juice tank is mounted on the basis of the former 2nd carbonation juice maturing tank.
Mnemonic scheme of the juice purification house
5) Liming tank before 2nd carbonation was left unchanged.
6) 2nd carbonation boiler: a new boiler of Series TC2-4.2 has been installed.
Juice purification station
7) 2nd carbonation juice maturing tank was made from the old Briegel-Muller prelimer.
8) For better mixing of lime milk and juice, the following units have been installed: dynamic mixer in front of the cold liming tank; static mixers before the main liming and in front of the liming tank before the 2nd carbonation
Dynamic mixer
Except for the circuits of the maintenance of levels and flow stabilization, the circuits of milk feeding, specified pH maintenance, suspensions returns and temperature conditions maintenance have been automated.
Juice purification trend
The scheme of Techinservice provides a high rate of chemical processes during the preliminary and main liming, generation of calcium carbonate during the 1st and 2nd carbonation with a high specific surface of sorption and adsorption capacity.
Juice purification trend
Techinservice automated two new 1st carbonation juice filters and one new 2nd carbonation juice filter installed by the sugar mill in 2012.
The existing quintuple-effect evaporating station was changed to the sextuple-effect evaporating station with the maximum use of low-grade heat transfer fluids and heat of secondary resources when syrup leaves the 6th effects with Bx 62-63 %. To obtain Bx syrup of 70-72 % before the vacuum pans, the syrup after the evaporating station is fully fed to the brown sugar melting mixers of the 2nd and 3rd products. The BMA sugar melting centrifuges of the 2nd and 3rd product were changed to the non-melting centrifuges. For boiling of the vacuum pans of the 1st product, secondary steam of the 3rd effect of the evaporating station is used, for boiling of the vacuum pans of the 2nd and 3rd products, secondary steam of the 4th effect of the evaporating station is used, for steaming of the equipment of the sugar end, secondary steam of the 1st effect of the evaporating station is used.
Heat of ammonia condensate is used for heating of runoffs of the sugar end, juice before the 2nd carbonation and limed juice. After cooling the ammonia condensate at the limed juice heat exchanger to a temperature of 68-72 °C, the condensate is distributed to the feed water tank for diffusion and the tank of other consumers. Condenser water is not used for feeding the diffusion units.
Mnemonic scheme of the evaporating station
Modernization of the heating scheme allowed achieving the steam consumption of 89 t/hour for a capacity of 8,000 tons of beet/day, consumption of fuel equivalent by weight of beet is 2.8% and by weight of sugar is 20.1%.
Filtering the syrup using five new TF150-65 filters with perlite alluvium produced by Techinservice allowed reducing the colour value of the syrup after the evaporating station by 3 times. At the same time, the quality of commercial sugar has significantly improved (haze was 8 icumsa).
The syrup can be filtered without perlite alluvium but in this case the used equipment should be of significantly more power.
The existing vacuum pans of the 1st and 2nd products in the sugar end have been modernized and fully automated. Techinservice has also introduced the seed massecuite system for boiling the 1st, 2nd and 3rd products.
Mnemonic scheme of the sugar end
Trend of the vacuum pan of the 1st product
Due to the implemented changes in the sugar end, the boiling time of the 1st product was 2.25-2.5 hours, the 2nd product was 3.5-4 hours and the 3rd product was 8-8.5 hours. The granulometric composition and colour value of commercial sugar have also been improved (colour value was 0.48 icumsa, average size was 0.79 mm, C.V. was 26.2%, haze was 8 icumsa).
A new fan cooling tower with an advanced spray system has been installed at the plant. This measure allowed for the maintenance of a stable temperature of chilled recirculating water, and accordingly rarefaction in the vacuum system without pumping river water.
A new fan cooling tower with an advanced spray system has been installed at the plant. This measure allowed for the maintenance of a stable temperature of chilled recirculating water, and accordingly rarefaction in the vacuum system without pumping river water.
This measure allowed for consumption of limestone at the rate of 3.1% by weight of beet for production.
Mnemonic scheme of the limestone house
Trend of the limestone house
The achieved results after modernization of Gaisyn Sugar Mill by Techinservice
Parameter |
Unit |
|
The capacity of the plant |
tons of beets/day |
8000 |
Consumption of fuel equivalent by weight of beet |
% |
2,8 |
Consumption of fuel equivalent by weight of sugar |
% |
20,1 |
Steam consumption for production |
т/час |
89 |
Haze of commercial sugar |
icumsa |
8 |
Colour of commercial sugar |
icumsa |
0,48 |
Average size of sugar granules |
мм |
0,79 |
Consumption of limestone for production |
% by weight of beet |
3,1 |